Blog #4
- harrisonngo1
- Nov 22, 2023
- 2 min read
Our final design consists of a top arm that adjusts for different size wheels. The arm will have rollers, allowing the user to rotate the wheel and handle the load from the wheel. The middle will be an existing scissor lift we intend to purchase. This scissor lift allows the device to comply with collapsed device volume constraints while being able to raise the wheel to 12”. The scissor lift is rated for loads up to The bottom of the design, which will be a base with wheels so we can roll the device around.
From November 11-25, the team made a CAD model of the final design and conducted load analysis. We also performed FEM analysis on the adjustable arm of our device. Since we planned to lift 100 lbs wheels, we used a load of 100 lbs. distributed along two rollers for our FEM analysis. We found that the maximum stress was 120 MPa, while the yield strength of structural steel, which we are making the arm out of, is 218.5 MPa. The safety factor is approximately 2, which is adequate for our device. We also found the max deflection from our FEM analysis, which was 1.4 mm at the end of the rollers. This is very little compared to the diameter of the rollers, so our FEM analysis found that the arm could handle the load from a 100 lb. wheel. We also finalized our budget.
Now that we have completed the analysis and finalized our design, we need to start ordering the items on our budget and gathering the necessary tools to fabricate our device. We plan to complete these tasks before the Spring 2024 semester. We plan to actually start building our project in the Spring 2024 semester.
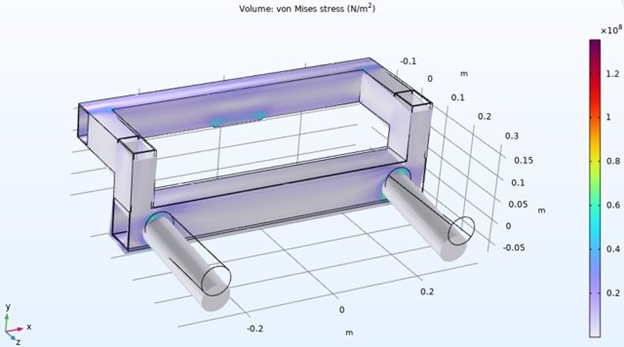
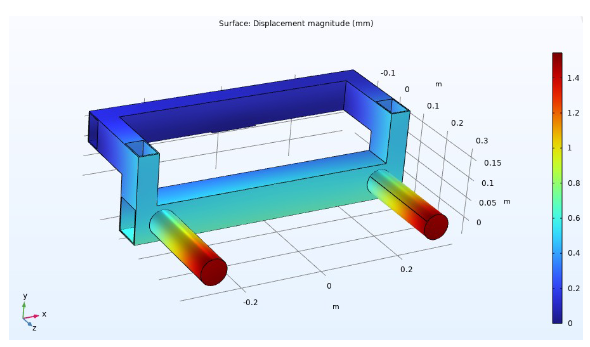

Comments